Quels matériaux sont utilisés en paramoteur ? D’où proviennent-t-ils et qu’advient-t-il d’eux en fin de vie ? Peut-on utiliser des matériaux recyclés ou naturels ? Sont-t-ils réparables ? Des questions bien dans l’ère du temps pour remédier à la raréfaction des matières premières en attendant une hypothétique économie circulaire des matériaux. Par Vincent Chanderot, PM+66
Les Suspentes
Les fibres aramides (dont les noms commerciaux sont Kevlar ou Technora) sont des polyamides aromatiques obtenues en pétrochimie par des condensations multiples du chlorure de téréphtaloyle et de la p-phénylènediamine.
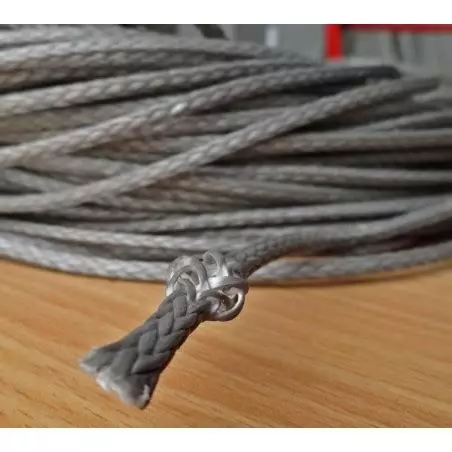
Les suspentes en aramide sont appréciées en paramoteur pour leur résistance aux hautes températures, en cas de contact avec le moteur. Pour cette raison, une solution courante de recyclage en fin de vie, après effilochage et découpe (pas évidente), réside dans les vêtements de protection contre le feu et la chaleur ou les plaquettes de freins. Les entreprises spécialisées dans le recyclage de l’aramide apprécient surtout les gilets pare-balles pour la quantité de fibre que chacun renferme, très supérieur à celle dans un cône d’aile. On peut aussi en faire des joints ou du matériau de charge pour renforcer les thermoplastiques.
Le Dyneema est aussi utilisé dans les suspentes (parapente surtout), les amarrages de suspentes, les sangles de secours et les connects. Il s’agit d’un polymère d’éthylène à chaîne extrêmement longue (UHMWPE pour ultra high molecular weight polyethylene). L’inventeur du Dyneema, DSM, a dévoilé cette année une version biosourcée de cette molécule longue mais simple, obtenue à partir d’un coproduit de l’industrie papetière, l’huile de Tall. DSM ambitionne de créer une économie circulaire du Dyneema d’ici quelques années, c’est-à-dire de pouvoir réutiliser les fibres en fin de vie dans la fabrication de nouvelles sans perte.
Le fabricant Liros met à disposition des boîtes afin de récupérer et recycler tous ses cordages.
Les voiles
Nous décrivions dans PM+58 le vieillissement des tissus. Les ailes sont très bien réparables auprès d’un atelier de couture qualifié, cependant l’obsolescence et la déformation des profils sont irréversibles.
Les tissus de parapentes sont fabriqués en fibre Nylon enduite de polyuréthane.

Le Nylon est une appellation commerciale, passée dans le langage courant, du polyamide 6 (PA6), ou polycaprolactame, obtenu par polymérsiation du ε-caprolactame. C’est un thermoplastique issu de la pétrochimie et sans filière organique connue. Son recyclage mécanique est aujourd’hui très commun, à partir de multitudes de filières telle que celle des filets de pêche usagés, par exemple, mais il génère une légère perte de qualité. Le processus de recyclage chimique ne subit pas cette perte de performance mais reste encore rare et coûteux. Aussi les fibres de PA 6 utilisées pour les ailes sont vierges, directement issues du pétrole. Les voiles ne sont pour l’instant pas recyclables dans la mesure où il est compliqué et pas du tout rentable de séparer le tissu de son enduction, ça n’est cependant pas impossible par voie enzymatique. Elles peuvent en revanche être upcyclées, c’est-à-dire réutilisées dans une autre destination. De nombreuses associations ou artisans se battent afin de récupérer des parapentes en fin de vie pour les convertir en sacs, housses, poufs, hamacs, rangements pour vans ou déco. Dans le windsurf, un grand classique est de transformer sa voile adorée mais détruite en abat-jour pour conserver à la maison cette lumière associée aux sessions magiques. L’anglais paracyclage propose aussi une vaste gamme d’accessoire et aussi de vous tailler une veste coupe-vent dans votre aile que vous trouviez si belle, ou pourquoi pas un pyjama dans un parachute de secours. Le fabriquant d’ailes Flyfat.ch taillait il fût un temps ses saucisse et pouf-bags dans des ailes usagées. La FFVL s’est aussi impliquée dans un projet de réutilisation des ailes pour en faire des planchettes de sellettes par compression.
Les sellettes
Le Polyester (PET) aussi utilisé dans les élévateurs, les combinaisons et les polaires se trouve très couramment en version recyclée (rPET), le plus souvent à partir de bouteilles d’eau. Comme pour tous les thermoplastiques, son recyclage chimique, qui le réduit à son état monomérique offre des performances supérieures au recyclage mécanique, mais il est encore rare. Rien ne s’oppose à l’utilisation du rPET pour toutes les pièces non structurelles ou d’habillage. La fabrication de fil recyclé consomme 80% d’eau et d’énergie en moins que pour le fil vierge, mais la phase la plus polluante se situe au niveau du tissage, les économies sur un produit fini sont donc au final de l’ordre de 10-20%. Par ailleurs ces tissus, s’ils sont lavés (on parle alors plutôt des vêtements techniques que des sellettes), relarguent tout autant de fibres micro-plastiques dans l’océan à chaque passage en machine.
Les Hélices
Un matériau naturel peut enfin trouver sa place dans le paramoteur : le bois. La dimension naturelle mérite toutefois d’être nuancée, car il s’agit de lamellé-collé. L’hélice est taillée dans un bloc constitué de lames de bois collées ensemble à l’epoxy, ce qui confère au matériau un surplus de rigidité et de résistance. Avec un bois issu de forêts locales gérées durablement ou labellisé FSC et un epoxy en partie biosourcé de type Sicomin greenpoxy on ne devrait pas être si mal.
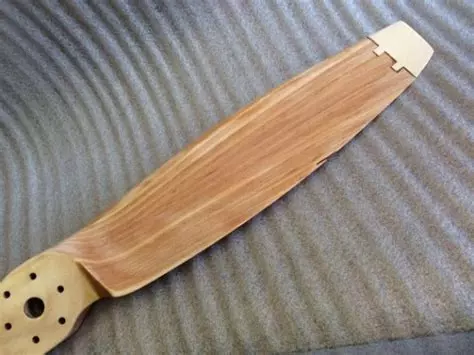
La fin de vie des hélices bois se passe le plus souvent en déco sur un mur ou en lustre, mieux vaut éviter de les brûler dans la cheminée. Avant d’en arriver là, ces hélices sont réparables, toutefois l’opération n’est pas toujours rentable au regard de leur prix relativement bas. De plus les interventions sont limitées, car le bois pompe beaucoup de résine : le gain de poids et l’équilibration peuvent devenir problématiques. Les hélices composites (carbone, verre, mais aussi lin) sont quant à elles réparables quasiment à l’infini et c’est souvent très intéressant financièrement, aux dires de Luc Dilé, réparateur d’hélices dans le Maine-et-Loire. Les petites altérations superficielles sont souvent prises en charge par les pilotes eux-mêmes, par exemple avec de la colle cyanolite et une charge de bicarbonate de soude, bien que ce ne soit pas idéal car les colles mono-composant tendent à se rétracter au séchage. Gare ensuite à l’ajout de masse qui risque toujours de déséquilibrer l’hélice. Les vibrations induites ne sont pas toujours faciles à distinguer des autres en vol et cela peut avoir des conséquences mécaniques préjudiciables.
Un morceau cassé peut être reconstitué si la rupture se situe au-delà de 20cm du moyeu. Les pales sont réusinées et ancrées chez Luc Dilé sous presse dans des moules créés pour chaque modèle, cependant il évite de retravailler les hélices bas de gamme creuses. Son atelier rachète des hélices délaissées par leurs propriétaires afin de les proposer reconditionnées sur le marché de l’occasion et si elles ne sont pas récupérables, il les broie en poudre afin d’en faire un matériau de charge.
Les moteurs
Les pièces sont toutes métalliques : Acier, aluminium, zinc, magnésium et tous ces métaux sont recyclables. C’est une excellente chose, car les métaux sont issus d’activités minières et de processus très énergivores (fourneaux, electrolyse) pouvant être réduits de façon colossale grâce au recyclage. Cependant, rares sont les métaux à être utilisés purs : ce sont généralement des alliages.
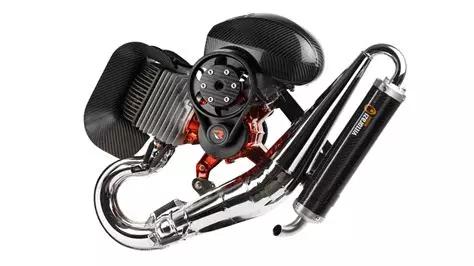
Les copeaux et les chutes issus de la première fonte se verraient perdre certaines de leurs caractéristiques, par conséquent ce qui est récupéré après la coulée n’est jamais remis dans le four, mais part en second choix. Le métal recyclé est utilisé sans limites pour les pièces sur lesquelles ne s’appliquent pas d’impératifs de sécurité. En raison des impuretés, notamment ferreuses que peut contenir l’aluminium recyclé, celui-ci est utilisé de préférence en fonderie (la pièce est formée dans un moule) et en filage (le métal est comprimé devant un orifice pour créer un profilé ou un tube) plutôt qu’en étirage (la pièce est formée par torsion entre deux enclumes) ou laminage (formation de plaques ou de feuilles entre deux presses cylindriques). Les vendeurs de tondeuses à gazon sont tenus de les récupérer en fin de vie afin de les dépolluer et les recycler. Cette opération est financée dès l’achat par l’Eco-participation affichée sur l’étiquette, mais elle n’est pas encore arrivée au paramoteur, par conséquent un moteur hors d’usage doit être déposé en casse ou en déchetterie une fois purgé de tous ses liquides (sans quoi il est considéré comme un déchet dangereux). Des « terres rares » peuvent être utilisées dans certaines pièces, notamment les aimants neodyme-fer-bore des démarreurs ou moteurs électriques. Les terres rares sont des métaux extraits difficilement en générant une pollution importante que pendant longtemps, peu d’autres que les chinois ont toléré sur leur sol, aussi en sont-t-ils devenus les producteurs incontournables et les tensions sur ce marché nombreuses.

Les carburateurs en Zamak sont constitués de Zinc avec de l’alu, du manganèse et du cuivre. Les alliages d’aluminium contiennent une teneur spécifique en Silicium, mais aussi d’autres métaux : Magnésium, Titane, Fer, Manganèse, Nickel, Zinc et Cuivre. C’est un métier très pointu que de parvenir à trier les métaux afin d’en restituer des lingots les plus purs possibles, mais il est difficile d’y parvenir à 100%, d’autant que certains éléments tels que le magnésium peuvent s’évaporer en fonderie. Par conséquent, avec les inconnues sur l’évolution des éléments résiduels, Bidalot nous dit recourir comme toute l’industrie aéronautique à du métal de première coulée, c’est-à-dire « neuf » pour les pièces de moteur et de structure.
Les Chassis
Chez le béarnais P2Air, qui conçoit et fabrique lui-même ses châssis, on considère que l’inox est le meilleur compromis poids/solidité/prix. Il se crée à sa surface de cet acier à forte teneur en chrome une couche d’oxyde de chrome le protégeant de l’oxydation. Il est souvent associé à du molybdène, nickel, tungstène, vanadium et titane afin d’améliorer ses performances. La section d’un chassis, si elle est de 14 en tubes inox, devra, pour atteindre la même solidité, monter à 16 en tubes titane et à 20 en aluminium auquel il faudra en plus ajouter des renforts. Par conséquent pour la course au poids, il ne suffit pas de s’intéresser qu’au poids moléculaire du matériau… Le titane est un métal très noble. Il est léger, plus dur que l’inox mais plus tendre également, il s’use davantage aux frottements. Il se redresse très bien après déformation, ce qui n’est pas possible avec l’aluminium. Sa soudure n’est pas des plus évidentes car, doté d’une forte affinité pour l’oxygène, il s’oxyde et une soudure réalisée à l’air libre devient cassante. Une belle soudure bien blanche et brillante réalisée sous atmosphère protectrice (d’argon) garantit sa solidité.
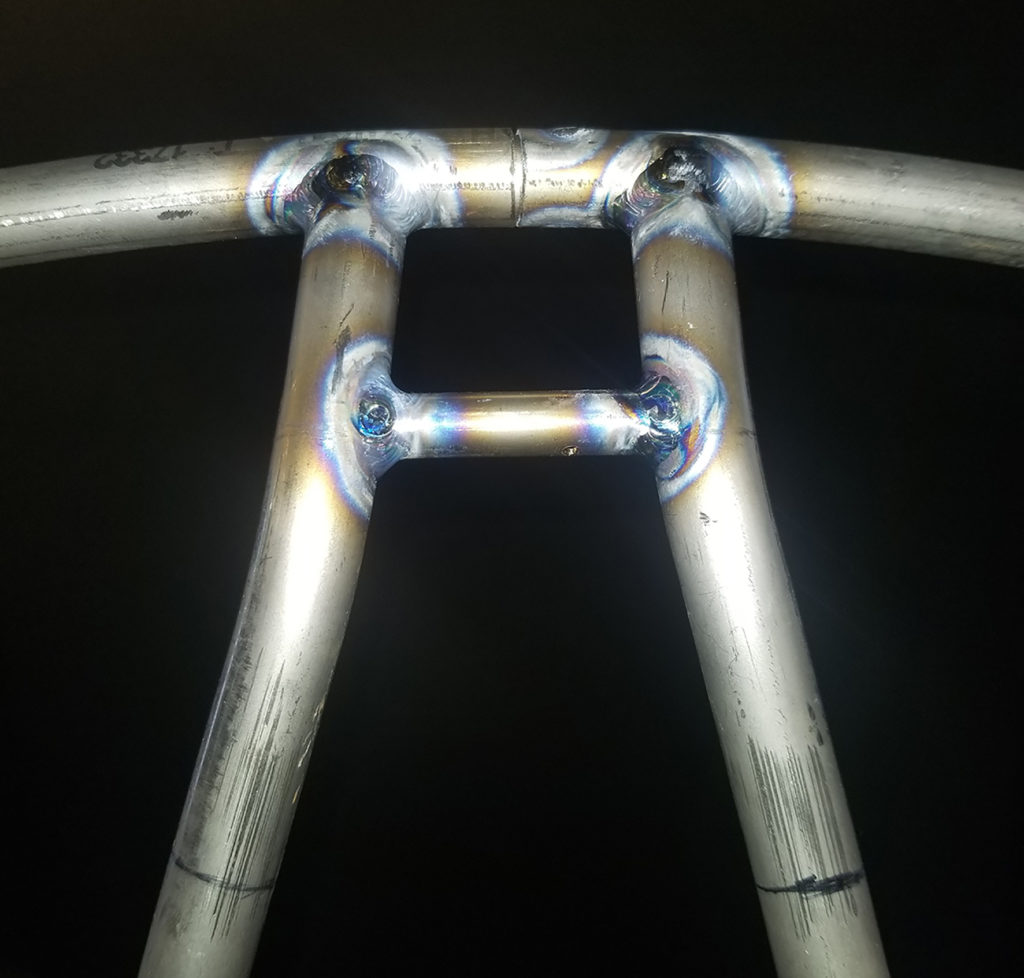
Titane et inox disposent des mêmes potentialités de recyclage que les autres métaux, mais aussi des mêmes inconvénients. On trouve aussi des pièces en matériaux composites. Il s’agit de résine durcissable renforcée par une fibre, de carbone ou de verre. Le verre résiste bien à la flexion, tandis que le carbone, plus léger et rigide, est beaucoup plus cassant. La fibre de carbone est tressée suivant plusieurs techniques à partir de dérivés du pétrole, mais il est aussi possible de la fabriquer depuis une base végétale, toutefois suivant un protocole assez polluant. Il existe une fibre naturelle, non traitée, très performante et dotée d’une excellente capacité d’absorption des vibrations : le lin, utilisé déjà sur les surfs. Les résines polyester et epoxy ainsi que leurs durcisseurs sont purement pétrochimiques, cependant les « greenpoxy » biosourcés à 75% ont changé la donne ces dernières années. Elles sont tellement performantes qu’elles sont utilisées en routine dans toute l’industrie du nautisme. Les composites sont légers, ils ne plient que très peu et rompent mais sont réparables, comme l’est une coque de bateau. La difficulté est ici de trouver un atelier qui prendra cette réparation en charge, d’autant plus qu’il s’agit d’une sacrée responsabilité d’assumer la réparation d’un bras oscillant en carbone ou de n’importe quelle pièce à laquelle on se suspend 1000m au-dessus du vide.